发动机连杆有限元分析优化
1 前言
汽油机连杆作为关重的 5C 件之一,承受拉压和弯曲组合载荷作用,承载变化剧烈,设计上应保证其有足够的刚度和强度。连杆组件主要结构包括:连杆体(也称为杆身)、连杆盖、连杆螺栓、大头轴瓦,有些连杆有小头衬套和定位销。连杆螺栓有两种结构形式,如图 1 所示。左图形式的螺栓从杆身肩部的螺纹孔穿入,另一端用螺母拧紧,连杆螺栓孔内并无内螺纹;右图形式的螺栓从连杆盖侧的螺栓孔穿入,杆身的螺栓孔内有内螺纹。两种结构形式的最大区别是杆身肩部的几何,前者刚度较弱,是疲劳失效的关键区域之一。
本文将针对这两种不同形式连杆的强度及优化进行对比。
2 分析过程
由于连杆的对称性,一般有限元建模都只用 1/2 模型以降低求解规模,节省计算时间。网格划分时连杆体、连杆盖、螺栓使用 C3D10M 单元,轴瓦、活塞销、曲柄销使用 C3D8I或者 C3D6 单元。接触对包括:连杆体-连杆盖、螺栓头部-连杆体、螺帽-连杆盖(对第 2种形式的螺栓为螺栓头部-连杆盖)、轴瓦-连杆、上瓦-下瓦、曲柄销-轴瓦、活塞销-连杆小头(或衬套)等。螺栓预紧力采用最小螺栓轴力,在相应位置的接触对中设置过盈或间隙。有限元模型如图 2 所示。
2.1 边界条件&载荷步
连杆的载荷主要以燃气爆发压力和惯性力为主,最大拉伸载荷出现在进气冲程开始的上止点附近,其数值为活塞组件和计算断面以上那部分连杆质量的往复惯性力
[1]
P' (m m )(1 λ)rω
t = + + 2
p s
其中,mp为活塞组件质量,ms
为计算断面以上的连杆质量。
最大压缩载荷出现在膨胀冲程开始的上止点附近,其数值等于爆发压力减去上述的惯
性力。
P' = − '
c P P
z t
另外,连杆为一长杆件,在压缩载荷下会发生平面内的弯曲,同时由于连杆摆的角加速度和转动惯量引起的惯性力矩,都会使连杆承受弯曲应力,但多数分析都没有考虑弯曲作用,且直接把最大压缩载荷考虑在 0 度曲轴转角,最大拉伸载荷考虑在 360 度曲轴转角。
本文中的连杆分析也采用这种处理方式,加上螺栓预紧力,共有以下计算载荷步:
1)、step1 螺栓预紧力及轴瓦过盈及间隙加载工况
2)、step2 最大扭矩点最大压缩载荷工况
3)、step3 额定转速点最大压缩载荷工况
4)、step4 零负荷工况
5)、step5 最大扭矩点最大拉伸载荷工况
6)、step6 额定转速点最大拉伸载荷工况
其中,step2 和 step5 构成一组疲劳分析对,step3 和 step6 为另一组疲劳分析对。
2.2 计算结果
从图 3 和图 4 的疲劳计算结果可以看出,连杆 1 容易在连杆体肩部圆角过渡处产生应
力集中,是安全系数较低的区域,而连杆 2 则发生在连杆盖的圆角过渡区。两个部位的最
小安全系数分别为 1.29 和 1.32,低于 1.5 的设计要求。
图 3 连杆体肩部圆角安全系数 图 4 连杆盖圆角安全系数
3 优化及效果
针对两个结构形式不同的连杆,首先研究其结构特点,对于连杆 1,肩部圆角处安全系数低主要是由于圆角至大头孔的距离过小,该处的抗变模量低造成,如图 5 所示,而其连杆盖圆角安全系数高则是由于在连杆盖处有一个凸起的设计,恰好能提高这个位置的刚度。反观连杆 2,由于连杆体肩部设计过渡良好,肩部到大头孔的距离表明该连杆在这个位置的抗弯能力足够。只是在连杆盖螺帽贴合面的圆角处因为有应力集中,同时又缺少象连杆 1 那样的加强凸台,因此安全系数偏低。
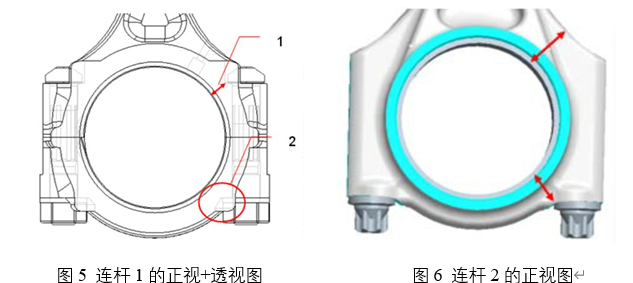
针对两个连杆的各自特点,分别制订的优化方案如图 7 和图 8 所示。连杆 1 的设计优化对连杆体而言只是改变了连杆体的机加工深度,但是连杆螺栓因为长度的变化需要重新招标生产。对连杆 2,连杆盖上凸台的增加需要对模具进行修改,但如果是在设计初期,则不会造成模具的损耗和浪费。优化后两连杆的最小安全系数均超过设计要求,其中连杆1 肩部圆角最小安全系数由 1.29 提高至 1.69,连杆 2 杆盖圆角最小安全系数由 1.32 提高到 1.58,如图 9、图 10 所示。
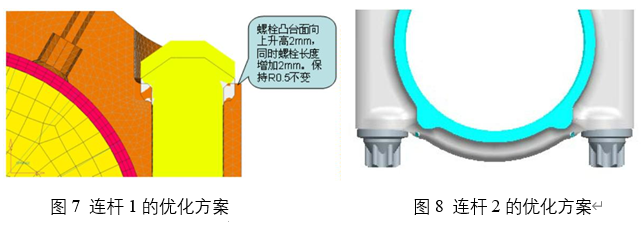
4 结论
(1)如连杆 1 形式的设计应力和疲劳关注区域包括杆身、连杆体肩部及杆盖等,其肩部由于下沉面的原因,往往是最容易失效的区域,因此设计时应特别注意。
(2)连杆 2 形式的设计已成为当前的主流,杆盖的凸台设计也在很多产品上出现。它能很好的提高杆盖圆角处的安全系数。
(3)应用 ABAQUS 进行连杆强度分析已越来越成为主流。
近期我们将给宁波吉利罗佑发动机零部件有限公司进行关于《发动机连杆强度、疲劳分析》;《商用车车架强度、疲劳仿真》;《乘用车车身强度、疲劳分析》项目导航培训。