铰接盘结构优化分析
本项目的研究对象用户汽车铰接盘结构,分析其在不同工况下的应力及变形状态,并根据分析结果对其进行结构优化。下图为汽车铰接盘结构的原始3D几何模型,主要包括前盘、后盘以及轴承。
图1 原始几何模型
研究内容
装配关系按前视基准面分为三个装配体,即:旋转前盘,使前视基准面夹角分别为0°、35°和52°,如图2所示。
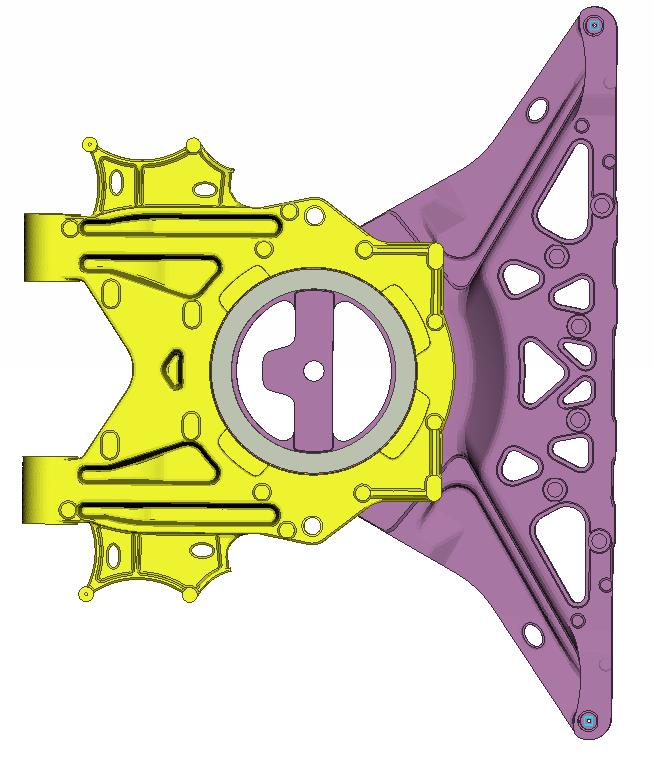
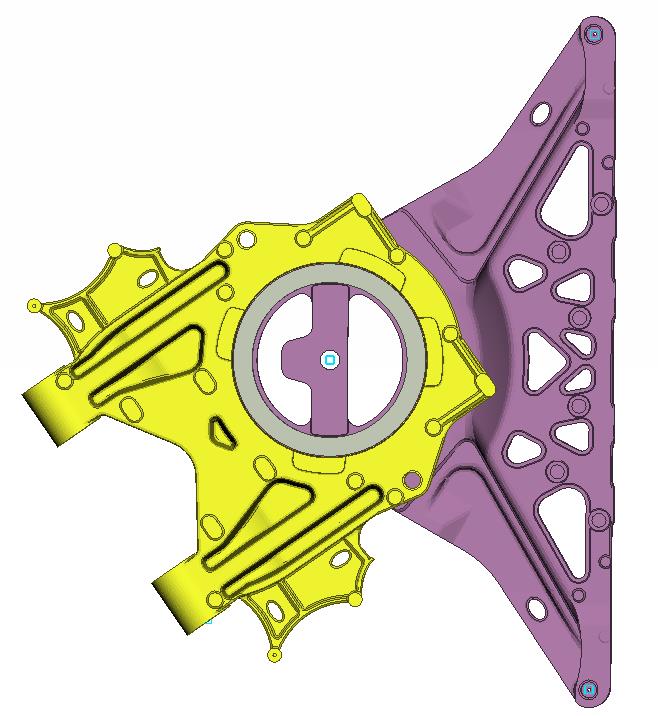
对于上述三种装配角度,分别参考表1载荷说明计算表2所示工况,其中A-E点位置参考图1。
表1 工况说明:
工况名 |
载荷位置和方向 |
载荷大小 |
垂直荷载工况 |
A和B同时施加,均垂直向下(Z轴负方向) |
|
扭转荷载工况 |
A处垂直向上(A处垂直向下) |
|
B处垂直向下(B处垂直向上) |
||
拉伸荷载工况 |
A和B同时施加,Y轴正向 |
|
新增工况1 |
C和D,沿CD连线,拉伸方向;E和F,沿EF连线,压缩方向,图示力方向(左、右同时) |
|
新增工况2 |
C和D,沿CD连线,拉伸方向;E和F,沿EF连线,压缩方向,图示力方向(左、右同时) |
|
表2 实际计算工况列表
工况号 |
工况描述 |
备注 |
1 |
0度装配角度,垂直+新增1 |
|
2 |
0度装配角度,垂直+新增2 |
|
3 |
0度装配角度,扭转+新增1 |
A向上,B向下 |
4 |
0度装配角度,扭转+新增2 |
A向上,B向下 |
5 |
0度装配角度,扭转+新增1 |
A向下,B向上 |
6 |
0度装配角度,扭转+新增2 |
A向下,B向上 |
7 |
0度装配角度,拉伸+新增1 |
|
8 |
0度装配角度,拉伸+新增2 |
|
9 |
35度装配角度,垂直+新增1 |
|
10 |
35度装配角度,垂直+新增2 |
|
11 |
35度装配角度,扭转+新增1 |
A向上,B向下 |
12 |
35度装配角度,扭转+新增2 |
A向上,B向下 |
13 |
35度装配角度,扭转+新增1 |
A向下,B向上 |
14 |
35度装配角度,扭转+新增2 |
A向下,B向上 |
15 |
35度装配角度,拉伸+新增1 |
|
16 |
35度装配角度,拉伸+新增2 |
|
17 |
52度装配角度,垂直+新增1 |
|
18 |
52度装配角度,垂直+新增2 |
|
19 |
52度装配角度,扭转+新增1 |
A向上,B向下 |
20 |
52度装配角度,扭转+新增2 |
A向上,B向下 |
21 |
52度装配角度,扭转+新增1 |
A向下,B向上 |
22 |
52度装配角度,扭转+新增2 |
A向下,B向上 |
23 |
52度装配角度,拉伸+新增1 |
|
24 |
52度装配角度,拉伸+新增2 |
|
后盘圆角结构改型说明
对原始模型进行计算,分析恶劣工况(工况1)结果,后盘两圆角处应力略有超标,应力最大值为357.5MPa,超材料屈服强度(320MPa),如下图所示。通过与委托方沟通,结合工程经验,考虑增大该处圆角半径,以此改善该区域应力环境。
调整过程
后盘圆角处原始几何:
左右两侧圆角调整方案相同,本报告计算模型及结果均为按上述思路调整后的模型。
结果
本章按24个工况的先后顺序,从前、后盘应力和变形的角度给出分析结果。(从分析结果来看,轴承内外圈应力级别与前、后盘在同一量级,但轴承材料屈服强度比前后盘大一倍以上,同时,轴承强度并不在此次分析评价的范围内,故仅给出前后盘结果。)
工况2
工况24
结论
项目通过对初始0°,35°以及52°装配角度的模型进行24个工况计算,首先找出应力超过材料屈服强度的位置,并提出修改建议,委托方给出新模型后,又对修改后的模型进行再次分析以及局部改型(报告第二章),经过两轮修改模型应力超过材料屈服强度区域明显变小。目前的分析结果表明,仅在后盘两侧圆角处以及减重孔边缘(垂直组合工况),前盘中间减重孔筋板边缘(扭转组合工况)有较小的区域进入塑性,其余区域在24个工况下均符合材料强度要求。
建议修改方案:后盘两侧圆角处圆角半径进一步增大(可参考第二章思路),后盘减重孔边缘有条件可考虑适当增厚;前盘中间减重孔筋板边缘,由于恶劣工况下,有较小区域应力超过材料屈服强度,因此,需保证其倒角工艺,若有条件亦可采用其他方法进一步降低该区域应力。